A drive shaft for every application
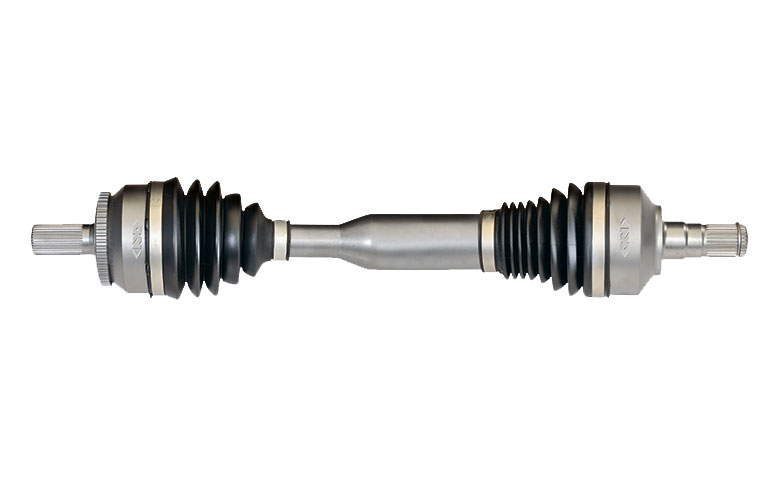
Each drive haft has two constant velocity joints – a fixed joint at the wheel end and a plunging joint at the gearbox end, connected by an interconnecting shaft
At Powell Shaft we appreciate the impact of these critical components on a vehicle’s dynamic performance, noise, vibration, harshness (NVH), durability, efficiency and weight saving, and their key role in enhancing power delivery, handling and comfort. Our advanced cardan shafts are the result of a continuing commitment to researching and developing new means to optimise and improve total performance.
We supply quality cardan shaft from OEM (GKN Shafts) from Germany which is a combination of experience, in automobile to process industries ranging from food production to steel and paper mills, in delivering power from stationary engines, electric motors and turbines.
Applications
Cement Crusher
Engine Dyno System
Wire Industries
Plastic Industry
Automotive
Railway Rolling-stock
Textile Industries
Pumping Station
Waste Water Treatment
Pulp & Paper
Steel Industrie
Drive shaft configuration examples
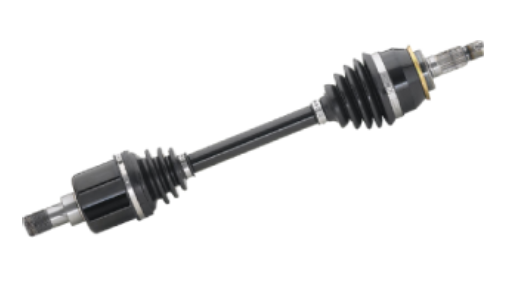
AC-Barshaft-GI
The combination of these joints with the solid barshaft represents the most common solution for front-wheel drive cars. The performance within reasonable installation conditions provides good NVH and durability for the majority of vehicles from A to D segment.
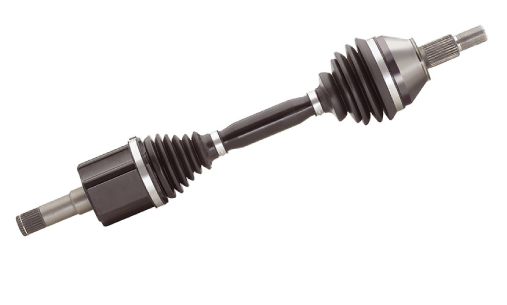
UF - Monobloc - AAR
This solution is chosen for more premium FWD applications where the UF joint provides high articulation for a small turning circle and the AAR joint allows higher installation angles with excellent NVH and durability performance. In combination with the MTS, the sideshaft is tuned for light weight, optimised stiffness and the highest level of ride comfort.
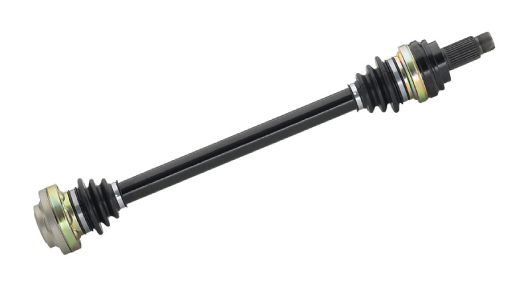
VL - Monobloc - VL
Sideshafts with this configuration are the preferred solution for premium RWD cars. The compact VL-joints with low backlash and optimised plunge resistance support the desired features of these vehicles. The use of the MTS allows for high torsional stiffness and light weight.
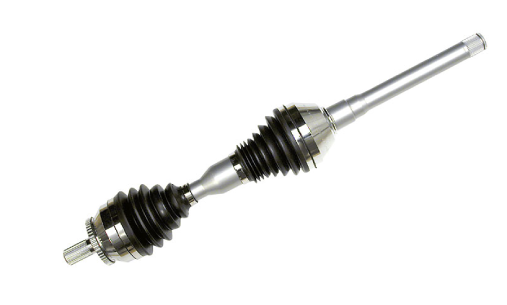
UF - Ballspline - UF
Sport utility vehicles (SUV) of the new generation are combining high levels of ride comfort with the occasional off-road capability. With the required suspension design and the resulting wheel travel, the performance requirement exceeds the traditional sideshaft design limits. The solution with UF-joints and a ballspline plunge device provides the necessary high articulation and long plunge capability to suit these applications. The ballspline also ensures the highest level of NVH refinement.
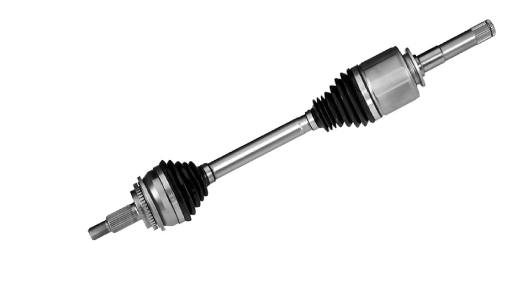
UF - Barshaft - DO
For very small and very large vehicles, the universal combination of UF- and DO-joints together with a solid barshaft is the recommended choice. Positive contribution of the UF towards achieving small turning circles and the versatility of the DO-joint for sideshaft applications are ideal for these vehicle segments. Suitability for manual and automatic gearboxes and feasibility for high installation angles come together with an acceptable NVH performance
Latest joint technology
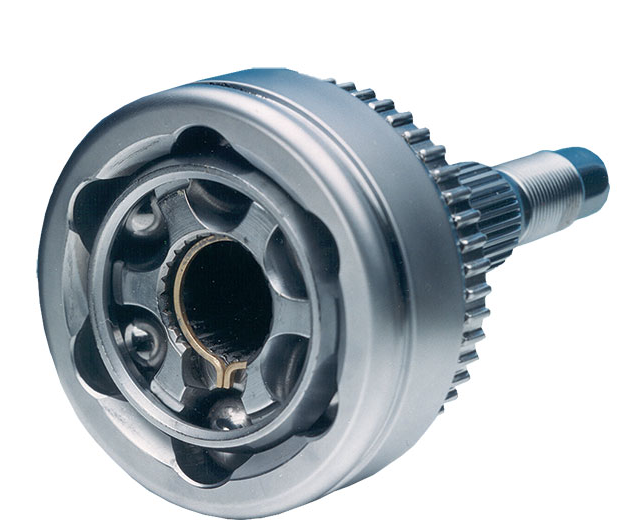
Fixed Ball (AC) Joint
The AC joint is suitable for passenger cars and light vehicles. Providing a maximum articulation angle of 47 degrees to meet the criteria for steering and suspension movement, it is the most popular choice for the wheelside of a constant velocity sideshaft.
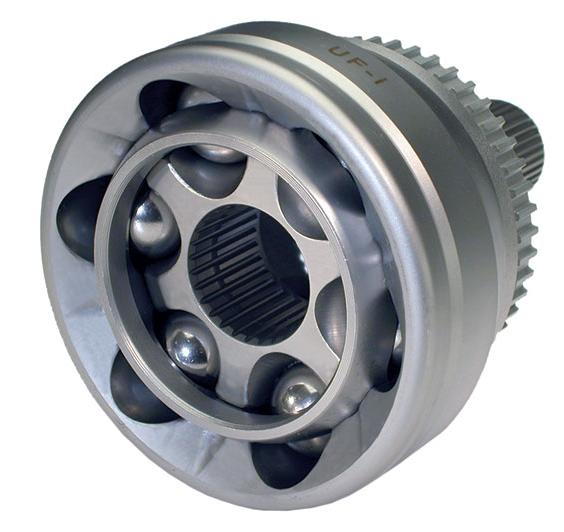
Fixed Ball (UF) Joint
Offering the same strength and durability as the AC joint, the UF fixed ball joint provides a maximum 50 degrees articulation angle, so affording greater latitude in the design of the steering geometry and facilitating smaller turning circles.
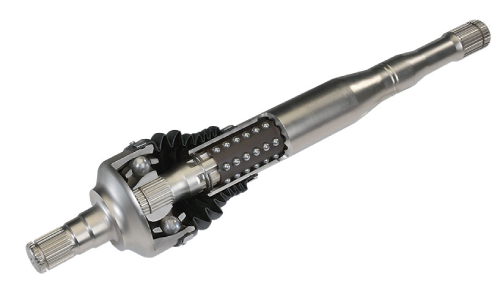
Fixed Ball Joint – SIO plus Ballspline
Sideshafts with this configuration are the preferred solution for premium RWD cars. The compact VL-joints with low backlash and optimised plunge resistance support the desired features of these vehicles. The use of the MTS allows for high torsional stiffness and light weight.
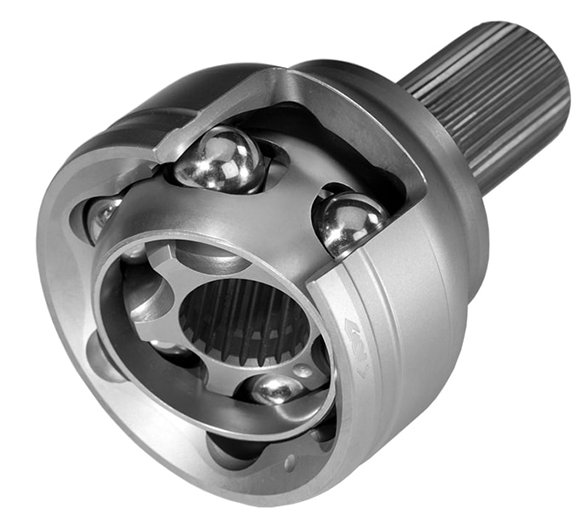
SX Countertrack Joint
SX joints are distinguished by a characteristic S-shaped track profile and counter-running ball tracks – hence the name “Countertrack”. This innovative design makes it possible to reduce internal friction, heat and size, as well as increase transmissible torque and maximum deflection angle (up to 52°).
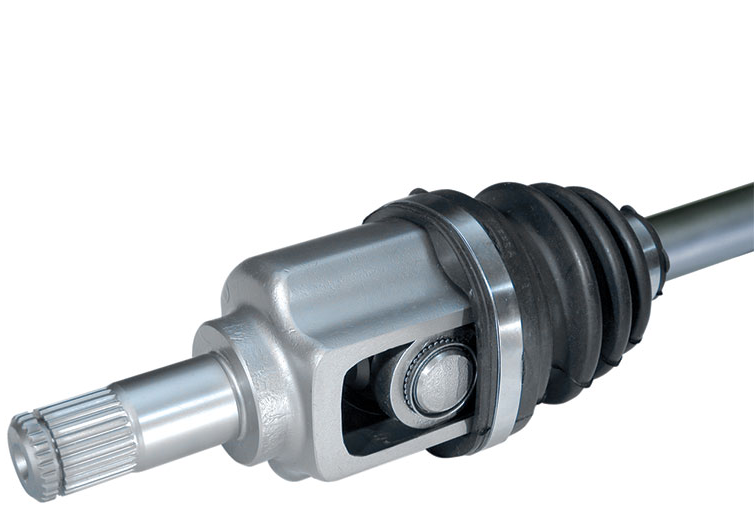
Tripod Plunging (GI) Joint
The standard tripod joint GI is suitable for the inboard gearbox joint of a constant velocity sideshaft for most vehicles. It has a maximum articulation angle of 23 degrees and has a plunge length of 50mm. It is ideal for medium working angles and its low plunge resistance aids good NVH characteristics.
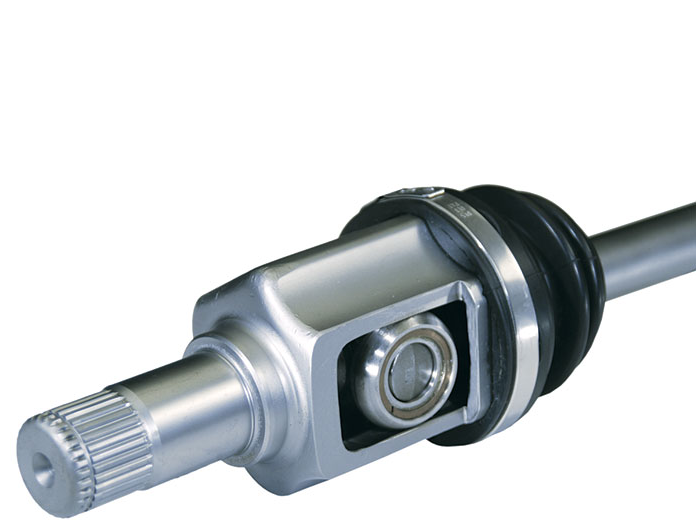
Tripod Plunging (AAR) Joint
In addition to the properties of the GI joint, the low plunging resistance and low axial forces of the AAR joint deliver additional NVH refinement, making it appropriate for high working angles. It has a maximum articulation angle of 26 degrees and 50mm plunge.
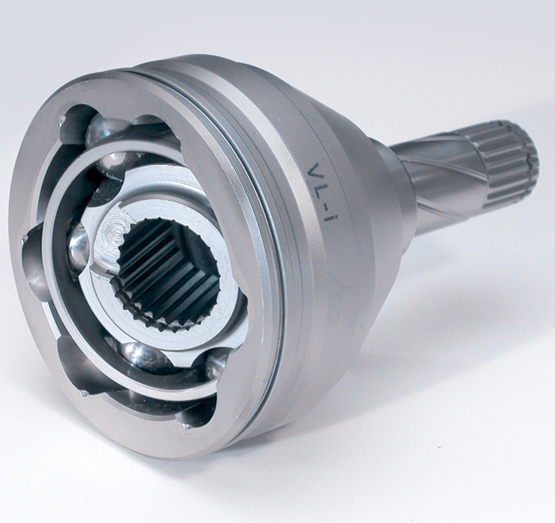
Ball Plunging (VL) Joint
The VL ball plunging joint is a popular choice for the inboard joint of rear-wheel drive CVJ sideshafts. With a maximum of 22 degrees articulation and a plunge of 50mm it is ideal for high working angles with low axial forces. The VL joint is also available as monobloc or disc version.
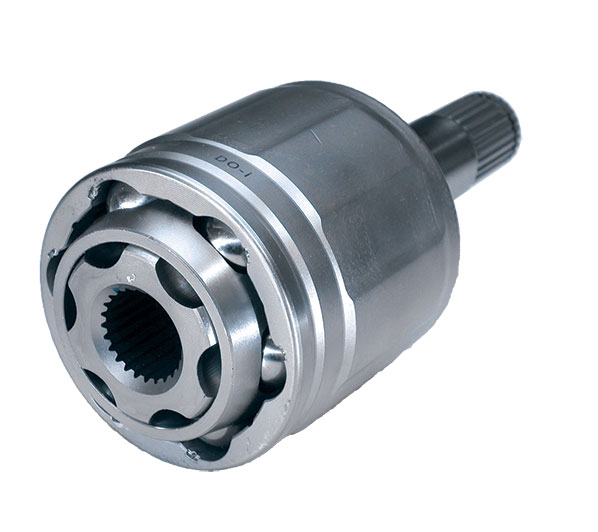
Ball Plunging (DO) Joint
The DO joint is similar to the VL. It is available in two versions with 50mm plunge for a maximum articulation of 26 degrees or 31 degrees. The DO joint is also suitable for high working angles on account of the low axial vibration.